Published on 2024-02-26
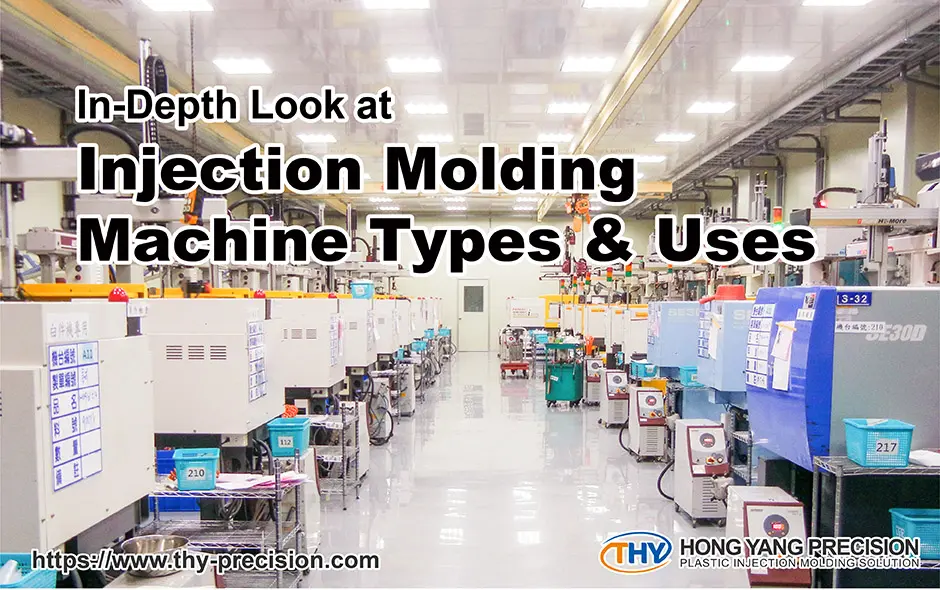
Injection molding, a crucial process in mass-producing plastic products, relies on specialized machines that handle material plasticizing, melting, injection, and ejection. This article explores the various types of injection molding machines, their key components, common applications, purchasing options, and maintenance considerations.
Table of Contents
What are the Types of Injection Molding Machines?
Injection molding machine types are frequently classified based on their drive systems. By understanding the strengths and weaknesses of each drive system, different types of injection molding machines can be chosen for various application areas.
- Hydraulic type
Hydraulic drives are used to secure the halves of the injection mold and to inject molten plastic into the mold cavity. These drives require hydraulic fluid and continuous energy for operating and cooling their hydraulic systems.
Despite its affordability, it is capable of meeting high precision requirements and can generate substantial clamping force. Hydraulic injection molding machines are typically used for creating larger, thick-walled products, like those in the automotive industry.
Yet, its reliance on hydraulic power requires frequent use and upkeep. If not operated regularly, the hydraulic injection molding machine may stop working.
- All-Electric type
The all-electric injection molding machine utilizes electrical servo motors to inject, extrude, clamp, and eject parts in the production.
Although it has a lower clamping force and is more expensive compared to its hydraulic counterpart, the all-electric machine excels in producing plastic parts with high precision (up to 0.01mm), cleanliness, and low noise levels. These attributes make the all-electric injection molding machine particularly well-suited for the manufacture of medical products in cleanroom environments.
- Hybrid type
Hybrid injection molding machines blend the best features of hydraulic and electric machines.They use servo motor pumps for the hydraulic fluid, which helps control power, emissions, noise, and energy use, and electrical power.
The cost of hybrid models fluctuates depending on size and application, but typically falls between the prices of electric and hydraulic injection molding machines.
Equipped with servo motors, these machines match the cost savings of all-electric models while enhancing user-friendliness and precision in clamping mechanisms, thereby reducing maintenance costs. However, it challenges technicians requiring both knowledge of electric and hydraulic operation systems.
New Technology: All-Electric Injection Molding Machines
If your ultimate goal is to achieve high precision and tight tolerance, All-Electric Injection Molding Machines would be the perfect choice to employ.
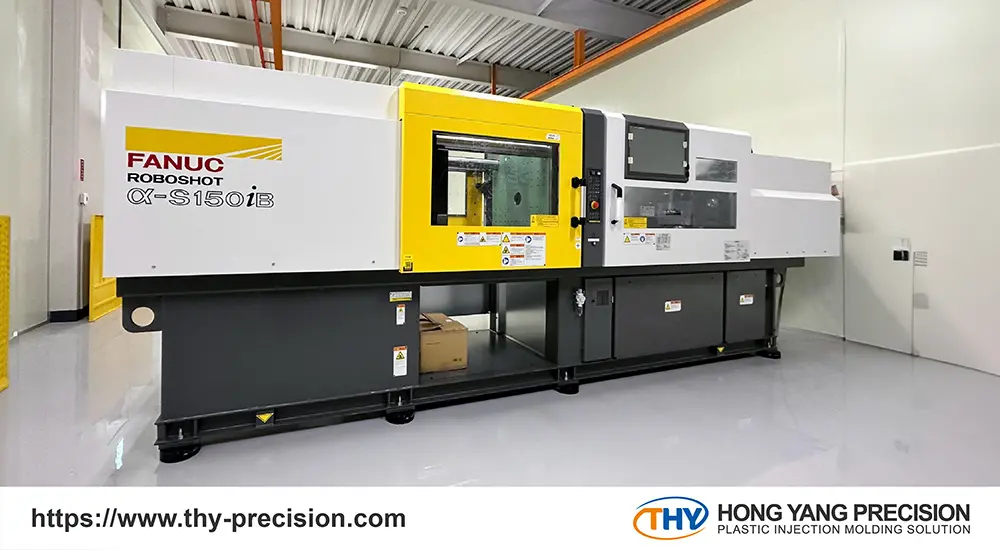
The all-electric injection molding machine presents numerous benefits, including cleanliness, precise control, consistent repeatability, efficient production, and precise automated manufacturing. This type of injection molding machine is the most ideal one to produce medical parts, optical lenses, or other products that have a high possibility to be used on the human body.
In terms of technical performance, notable advanced features are backflow monitoring, selective platen options, and low-friction linear guides.
- Backflow Monitoring
This feature enables users to monitor the wear on the check-valve, ensuring consistent product dimensions across large production volumes. It can effectively help prevent molding defect issues like shrinkage, deformation, and loose textures, maintaining product quality.
- Selective Platen
The machine offers two platen types for varied applications. A single platen configuration increases the mold space, while a double platen setup progressively enhances rigidity, catering to different molding needs.
- Low-Friction Linear Guide
The linear guide reduces friction, which is critical for smooth operations during molding. This contributes to the machine’s overall efficiency and precision in product creation.
Application of All-Electric Injection Molding Machines
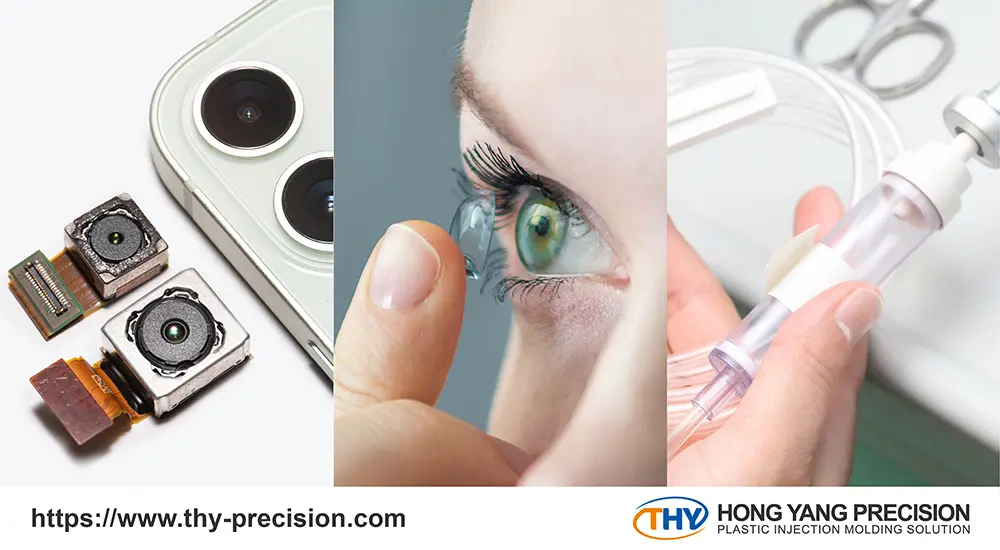
All-electric injection molding machines, known for their extensive benefits, are frequently chosen for applications requiring high cleanliness standards.
This type of injection molding machine differs from hydraulic injection molding machines, which use hydraulic oil, in that it offers a cleaner production environment by removing the possibility of oil leakage and contamination.
Consequently, an all-electric machine is exceptionally suitable for producing medical equipment, optical devices, and other products where a high degree of cleanliness is essential.
Prominent applications of all-electric injection molding include medical components, precision lenses, and thin-walled light guide panels, and the used materials are also varied based on manufacturing purpose. For instance, in the medical field, Cyclo Olefin Polymer (COP) is widely used for making syringes due to its heat resistance, high purity, and clarity.
In optical applications, COC is also preferred for its outstanding optical qualities, including excellent transparency, low birefringence, high Abbe number, and heat resistance, making it ideal for camera lenses.
Polycarbonate (PC), known for its high transparency, durability, and shatterproof qualities, is commonly used in smartphones as a light guide panel, offering a safer and effective alternative to glass.
Learn more about 10 Plastic Resins for Injection Molding: A Guide to Types & Uses
Your Partner in Injection Molding: THY Precision
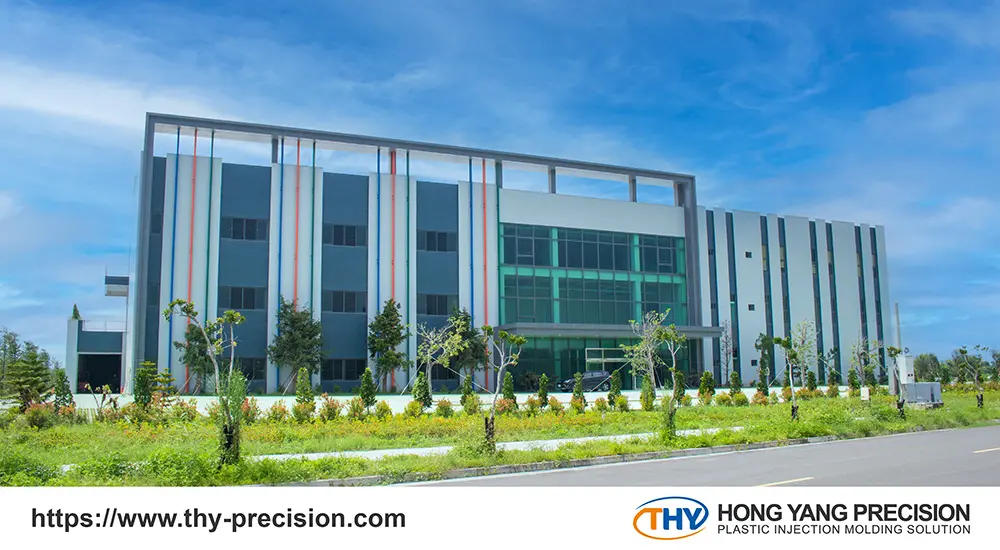
THY Precision stands as a distinguished manufacturer of micro optical parts, including micro-optics on non-flat substrates and plastic contact lenses. Our expertise extends beyond optics, marking us as a remarkable producer in the medical components industry.
At THY, the depth of experience in ODM/OEM manufacturing enables THY Precision to offer an all-encompassing One-Stop Service, tailored to meet clients’ specific needs. This service encompasses mold design, material selection, and assembly. THY’s commitment to quality is evident in their high-standard product validation, custom logo printing, and exceptional cleaning services, ensuring a client-centric and quality-driven approach.
THY Precision also excels in secondary services like ultrasonic welding, upheld in a high-standard cleanliness environment. This ensures the highest levels of cleanliness are maintained, mitigating any risks of contamination or quality degradation during the welding process.
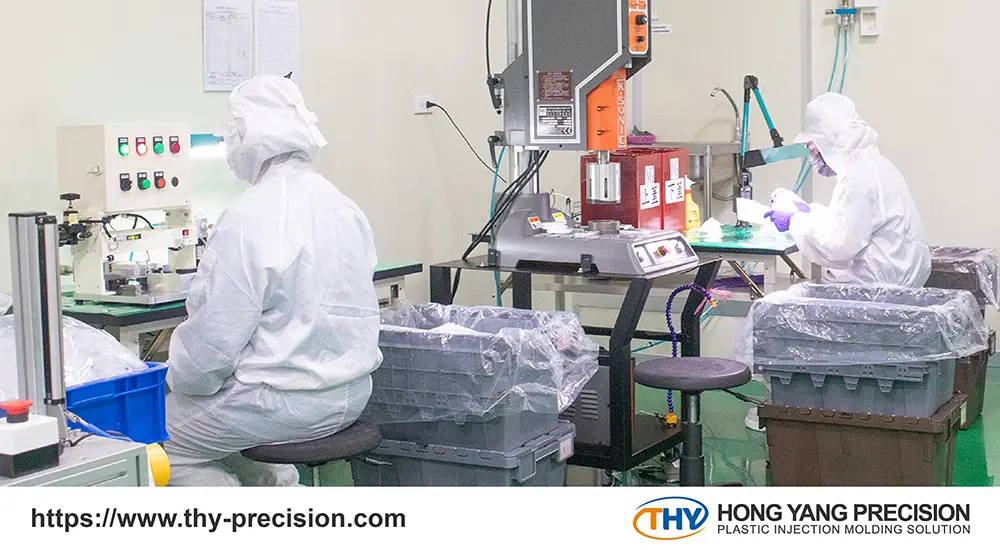
Should you have any inquiries or specific design needs related to high-standard, cost-effective products suitable for large-scale production, please do not hesitate to contact THY Precision.
We are ready to provide our experienced engineers who will engage with you to discuss your unique requirements and tailor solutions to your specific needs.