Published on 2024-03-13
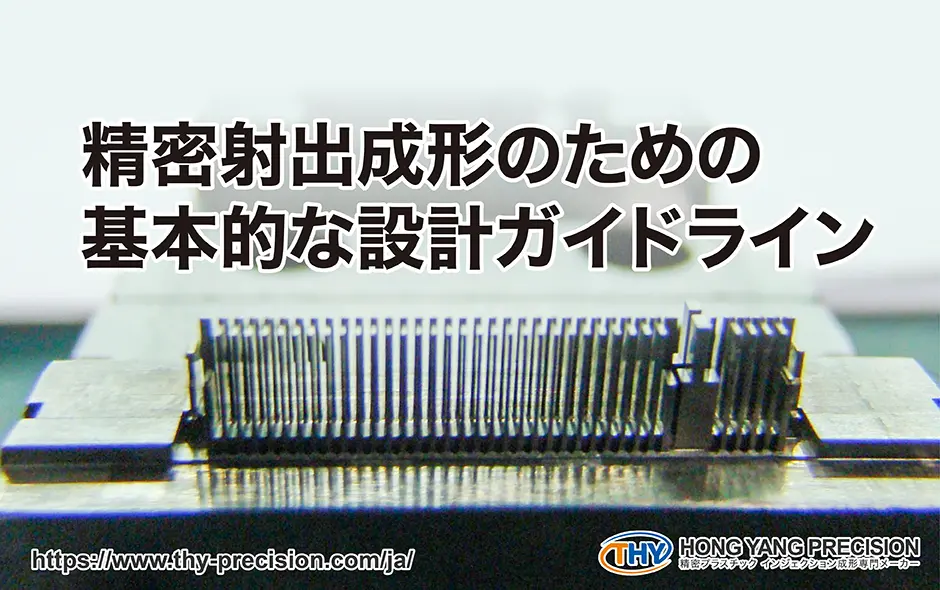
射出成形における一般的な設計ガイドラインと潜在的なリスクを理解することは、予期せぬ不具合やコストを防ぐために不可欠です。 この記事では、射出成形の主な設計ガイドラインを網羅し、射出成型プロセス中で頻繁に発生する問題点に注目します。
Table of Contents
精密射出成形の設計ガイドライン
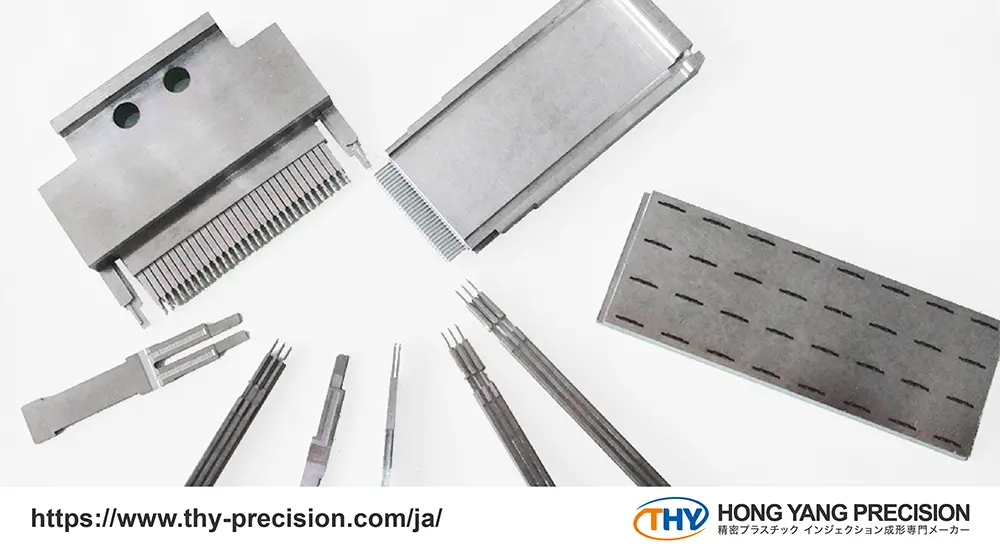
射出成形の分野では、製造不良や、生産コストが上がってしまう事を回避するため、特定の設計ガイドラインを遵守することが必要です。 ここでは、6つの重要なガイドラインとそれに対応する射出成形を成功させるのための設計ガイドラインを紹介します。
1. 抜き勾配(Draft)
適切に設計された抜き勾配は、射出成形品を金型から取り出す際の効率と品質両方を向上させます。 抜き勾配をしっかりとる事で、成形品が離型する際の削り取りや擦れを防ぎます。
抜き勾配の設計に関する一般的なガイドラインでは、金型の深さ1インチに対して1度の勾配を適用することが一般的とされています。 このアプローチにより、射出成形品への予期しない損傷を防ぐのに役立ちます。
2. 曲げ半径(Radii)
射出成形では、樹脂の特性により、鋭い角を回避するため曲げに半径をとることが重要です。 鋭い90度の角は、材料の流れを妨げ、製品の完全性を損なう可能性のある応力集中を引き起こす原因になります。 これを緩和するために、金型の角の設計にR/T比が適用されます。「R」は半径、「T」は隣接する壁の厚さを示します。
考慮すべき2つの種類の角があります:内角と外角。 一般的な応用では、内角はR/T比0.5で設計され、外角はR/T比1.5を採用します。 このように曲げ半径をつることにより、内角と外角の両方が材料の流れと構造の完全性が最適化されます。
![]() | ![]() |
---|---|
図1 半径加工前の金型 | 図2 半径加工後の金型 |
3.肉厚(Wall thickness)
肉厚は射出成形において重要な要素であり、完成品の凹みや反りに大きく関わります。
射出成形では幅広い材料が使用されるため、最適な壁の厚さを選択することは複雑です。 そのため、射出成形で最も使用されるトップ10の材料を選定し、それぞれの最適な肉厚の、推奨値をまとめました:
素材 | 推奨される肉厚(インチ) |
---|---|
アクリル (PMMA) | 0.025 – 0.150 |
ABS樹脂 (ABS) | 0.045 – 0.140 |
ナイロン (PA) | 0.030 – 0.115 |
ポリカーボネート (PC) | 0.040 – 0.150 |
ポリエチレン (PE) | 0.030 – 0.200 |
ポリオキシメチレン (POM) | 0.030 – 0.125 |
ポリプロピレン (PP) | 0.025 – 0.150 |
ポリスチレン樹脂 (PS) | 0.035 – 0.150 |
熱可塑性樹脂ゴム弾性体 (TPE) | 0.028 – 0.150 |
熱可塑性ポリウレタンエラストマー (TPU) | 0.020 – 0.200 |
4.アンダーカット(Undercuts)
アンダーカットとは、成形品を金型から取り出際、そのままの状態では離型できない設計を指し、具体的には以下のアニメーションにような状態をしまします:
アニメーションの左側は、アンダーカットのない、金型からのシームレスな取り出す事が可能な構造です。 逆に右側は、アンダーカットの特徴を持つ製品を示しており、この構造ですと完成品が金型に詰まってしまいます。
![]() | ![]() |
---|---|
アンダーカット無し | アンダーカット有り |
5.ゲート(Gates)
ゲートの位置とスタイルは、材料を金型キャビティに誘導するための重要な構造です。 ゲートは、材料が流れる力、角度、温度を考慮します。これらの要素は、最終成形製品の品質を形成する上で重要な役割を果たします。 ゲートの設計と機能の最適化を確実にするために、以下のガイドラインに従ってください:
- 干渉を防ぐためにコアとピンから距離を取る
- ゲートの取り外しを容易にするために、大きなスペースを確保する
- 品質を向上させるために、材料の流れる経路の長さを短縮する
- 複雑または大型の部品には複数のゲートを使用して、均一な材料配分を確保する
これらのガイドラインに従うことで、成形のできが向上し、品質の高い完成品を作ることができます。
6.エジェクターピン(Ejector pins)
エジェクターピンは、射出成形プロセスが終了した後に金型キャビティから成形品を取り出す役割を担うエジェクターシステムの重要な部品です。 他のエジェクションメカニズムと連動して、エジェクターブレードやブロックなど、成形後の部品が効率的かつスムーズに取り出されることを確認します。 エジェクターピンを選択する際には、最適な性能を確保するために、以下のガイドラインにしたがってください:
- 直径の大きなピンを選択する:直径の大きなエジェクターピンは、より安定したスムーズな取り出しプロセスを保証します。
- エジェクターピンのサイズを標準化する:可能な限り均一なサイズのエジェクターピンを使用するように心がけてください。これにより、複数のサイズに対応する必要が減り、設計プロセスが簡素化されます。 歪みのリスクを最小限に抑える:
- 押し出し時の曲がりや歪みを防ぐために、直径 2.5 mm を超えるエジェクタ ピンを使用することをお勧めします。 これにより、排出段階全体を通じて耐久性と安定性が保証されます
3つの表面の成形不良とその回避方法
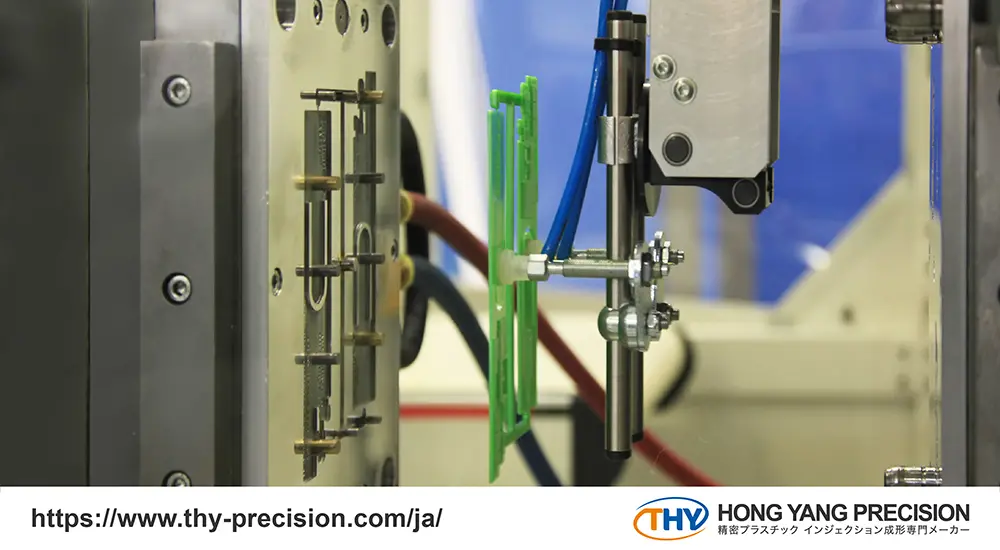
射出成形の領域では、先に述べた設計ガイドライン以外にも、完成品に生じる一般的な成型不良にも対処することが必要です。 これらの頻繁な問題を軽減するために、各欠陥タイプに合わせた設計ガイドラインを提供し、よりスムーズな射出成形プロセスを確保します。
1.割れ(クラック)
仕上がった製品のひび割れは、冷却後によく発生する現象です。 残留する内部応力によって表面が損傷してしまうのが原因です。
残留する内部応力によって表面が損傷してしまうのが原因です。この割れ現象の発生を防ぐには、いくつかの方法があります:
- 対処する方法は3つあります:
- 金型の温度を上げて内部応力を軽減する
- 充填時間を短縮し、金型のゲートのサイズを小さくする
また、特定の要因が割れの原因になることもあります:
製造に適切でない材料を使用すると、製品がひび割れる可能性があります。 例えば、PSを使用すると射出成形プロセス中に予期しないひび割れが生じることがあります。 この場合、問題を回避できない場合はABSなどの代替材料に切り替えるよう、ベテランエンジニアがお客様に提案します。
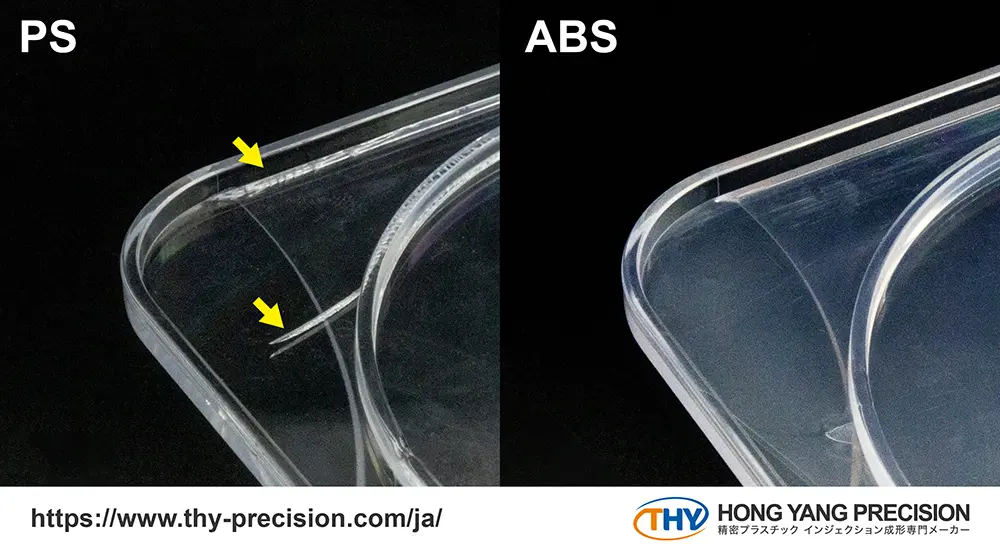
2.バリ
バリとは、射出成形製品の表面によくみられる成型不良であり、表面の滑らかな仕上がりを妨げます。 この現象は、金型の設計が不適切であるか、射出成形条件が不十分な場合に起こります。 以下の2つの解決策でバリを効果的に避けることができます:
- 射出成形条件が適切に設定されているか、改めて確認します。
- 射出中に雄型と雌型の金型がしっかりと締め付けられ、位置決めや表面の均一性が確保され、縁のついた部分が発生しないようにします
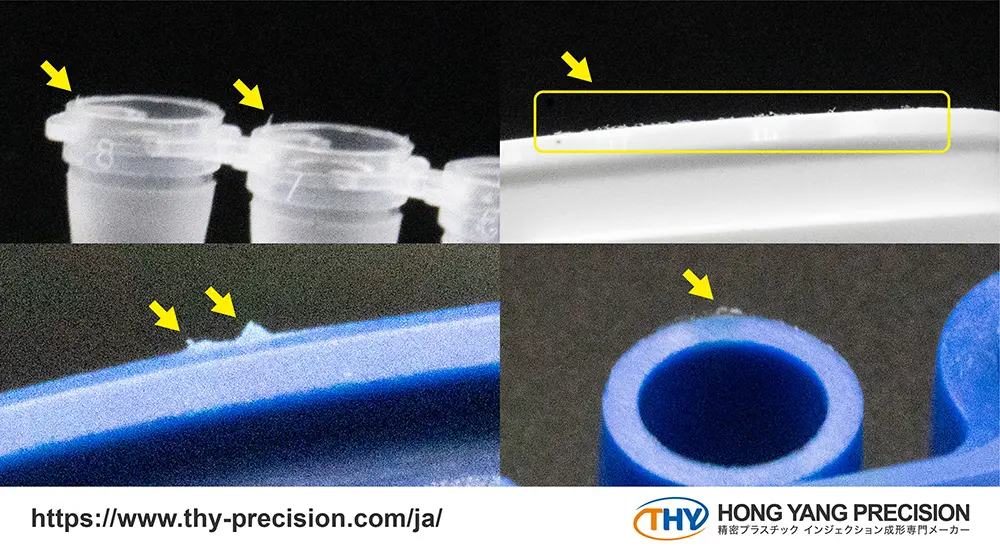
3.フローマーク
射出成形では、特に低い射出速度で、溶融材料が金型表面に接触した際に急速に冷却され、流れ抵抗が過度に生じることで、流れの先頭部分に歪みが生じる場合があります。
これにより、固化した外層がキャビティの壁に十分に密着せず、波状の外観(レコード状の溝)が生じます。 この波状のパターンが固化した後は、保持圧力がそれを修正することができず、この欠陥が恒久的に残ります。 エンジニアはこの欠陥を予防するために次の対策をとれます:
- 射出速度を上げる
- 金型の温度を上げ、金型内の温度差を防ぎます
THY精密工業で部品のデザインを具現化する
デザイナーやメーカーの専門知識がないと、製品開発の際コストが増加し、時間がかかることがあり、予期しない支出につながることがあります。
これらの課題を回避し、製品の収益性を高めるために、当社の経験豊富なR&Dエンジニアが射出成形の完全な設計ガイドラインを確立しています。 当社の目標は、お客様の製品を精密かつ信頼性の高いものにすることです。
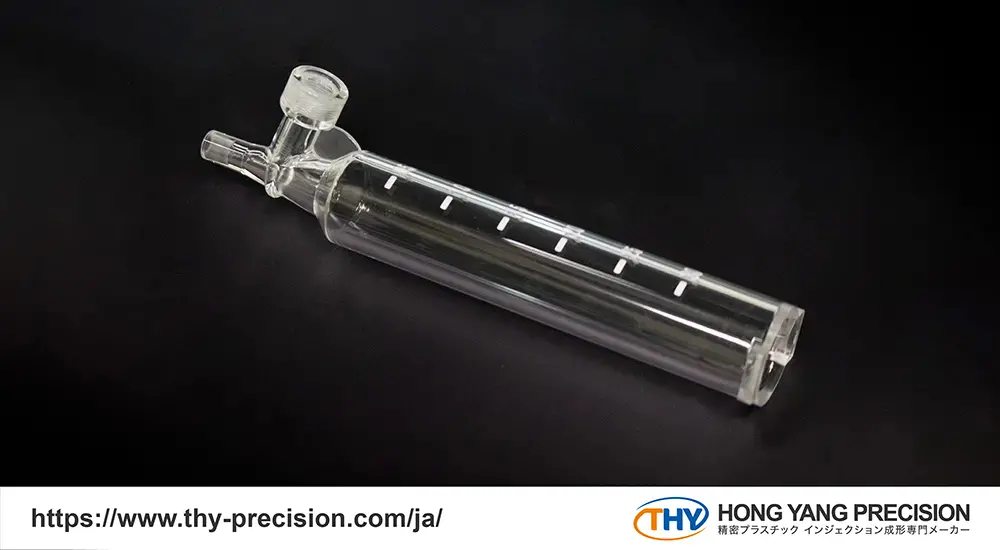
THY精密工業は、タイトな許容差(±0.001mm)の医療グレードおよび光学部品のメーカーとして、また汚染を防ぐためのハイグレードなクリーンルーム(クラス8およびクラス7)を提供しています。 さらに、当社はISO 9001およびISO 13485の基準を満たしております。
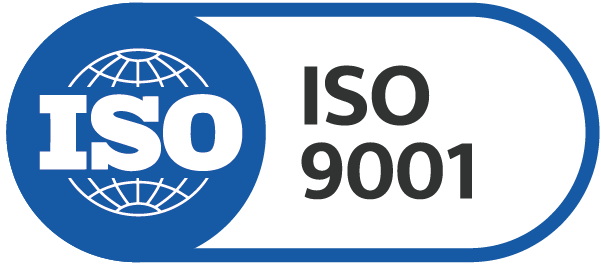
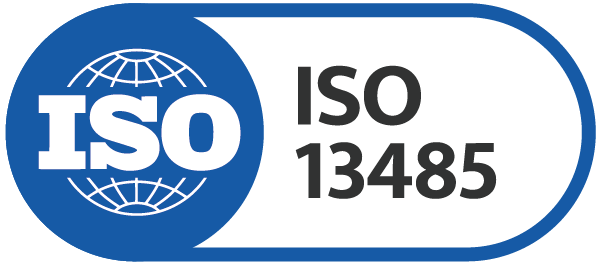
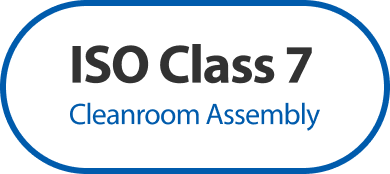
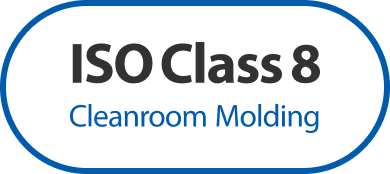
もし射出成形のデザイン上の課題や、製造のに関する需要がある場合は、お気軽にお問い合わせください。
射出成形についてもっと知る:
プラスチック射出成形を手順別に徹底解説
射出成形機の種類と用途例を詳しく解説